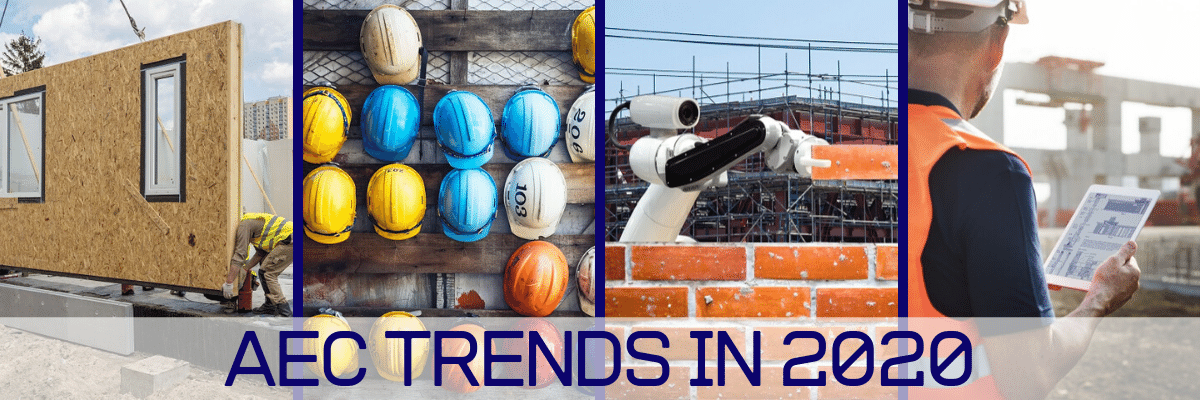
Change is inevitable, even in the construction industry.
Not only is change expected but it can also bring new and emerging business opportunities. Exploring and adopting these advances could be the catalyst you need to jump ahead of your competitors.
Modular Construction can Reduce Project Timelines by 20 – 50 Percent!
Among the trends to watch in 2020 is the move toward modularization and prefabricated components. Modular construction takes a prefabricated approach to building repetitive structures such as offices, apartments, and hotels. Off-site construction is a game changer, increasing productivity because:
- tasks can happen concurrently when they would have previously been completed sequentially
- avoids weather related delays
- enables more-efficient use of human capital as productivity in a central shop environment is higher than on a construction site
McKinsey believes offsite construction can increase the speed of construction by as much as 50% and reduce costs – if done in the right environment – by 20%. Modular Construction Market forecasts it will be valued at $157 billion by 2023, at increase of almost 50% in just 6 years. Modularization and prefabrication not only save on labor costs but might also ensure better quality, and shorten the project schedule, with less labor required on-site.
Decreased Labor Force – Not all Trends are Positive
With an estimated 250,000 unfilled construction positions in the United States alone, the labor shortage is expected to continue in 2020. Contractors continue to report difficulty finding workers and lengthy backlogs. According to ABC’s Construction Backlog Indicator (CBI) the average backlog stood at 8.9 months in October 2019.
Ask any contractor about their circumstances, and they are likely to lament about the inability to secure a sufficient numbers of electricians, plumbers, glaziers, roofers, superintendents or estimators. The effects of the skilled labor shortage can be seen in all areas of the construction industry. These shortages come at a time when, according to ABC’s Construction Confidence Index (CCI), 57.2% of contractors intend to expand their staffing levels for the coming six-month period, while just 8.3% intend to decrease their staffing levels.
Automation will Deliver Efficiencies Without Stealing Jobs
Robots, AI (Artificial Intelligence), and drones are not looking to replace jobs, rather the automated machines can improve productivity and accuracy while reducing waste and overhead. Considering the labor shortage in construction, they fill in the gaps allowing workers to focus on other tasks.
For example, the average bricklayer can put down about 500 bricks per day. Construction Robotics’ Semi-Automatic Mason, SAM is designed to work collaboratively with the mason, laying up to 3,000 bricks per day. Increasing the mason’s productivity by 3-5x while reducing lifting by 80%+. Robots like SAM can take on repetitive tasks while workers manage the equipment.
Artificial intelligence works in the same way, taking over the mundane tasks for greater accuracy, speed, and productivity. Construction sites use drones (also known as Unmanned Aerial Vehicles (UAV)) to survey the site, collect information for survey data, and verify workers stay out of potentially dangerous situations.
On-site workers don’t have to be worried that robots or other autonomous equipment will be stealing their jobs, according to World Economic Forum, robots, drones, and IA create as many new jobs as they displace.
Automation on construction sites, particularly of highly repetitive tasks, could significantly improve productivity while creating a safer work environment and helping to address the industry’s labor shortfall.
Embracing Technology will Set You Up Well for the Future
While McKinsey expects the productivity of construction companies to increase 20% in the next 5 years, this will only be the case for businesses that deploy the latest technologies and use them well.
Building Information Modeling (BIM), is proving to be an outstanding tool in commercial construction. For example, BIM can model complex work processes from the start, beginning with the design. This intelligent 3D modeling helps engineering, architecture, and construction professionals find a way to effectively plan, design, construct, and manage buildings and their infrastructure.
BIM technology can help identify areas of energy savings or better space usage throughout the building. BIM can display the entire HVAC system and run simulations to verify it works as planned, allowing it to be tweaked virtually, thus shortening construction time, and reducing the cost of making changes during the building stage.
Change is hard. The labor shortage is forcing the industry to explore more effective ways of tackling the same old problems. Investigating these trends could mean the difference between finishing on time and within budget or lagging behind.